Injury Incident Prevention
injury iNCIDENT PREVENTION
The University engages in a program of voluntary compliance with the Occupational Safety and Health Act of North Carolina and with all applicable federal, state, and local regulations and codes. To be effective, this program must be proactive and must embody the proper attitudes toward injury incident prevention on the part of all members of the University community.
Injury Incident prevention can be classified as a broad term that involves understanding your responsibilities, compliance with safe work practices, communicating safety issues, safety training, identifying workplace hazards, procedures for corrective action, and record keeping. All these efforts combine to prevent work-related injuries and illnesses to members of the University community. For more information, please review the University Incident Prevention PIM #26.
Slips, Trips, and Falls
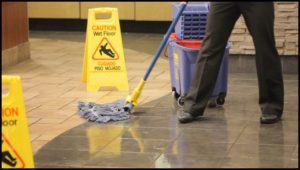
Slip, trip and fall incidences are some of the leading causes of occupational injuries at UNC Charlotte. It is very important that you, as an employee, remain aware of your surroundings. The following guidance provides general awareness about slips, trips and falls, contributing factors that cause them, and tips on preventing these types of incidents.
- Slips, Trips and Falls training
- Slips, Trips, and Falls Fact Sheet safety talk
- Remove the source of the slippery surface
- Clean up all spills
- Install caution signs
- Wear appropriate footwear
- EHS Safety Service Request to assess the hazard
Materials Handling
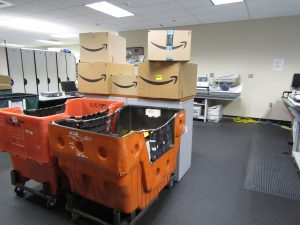
Materials Handling is one of the leading causes of occupational injury at UNC Charlotte. Therefore, it is very important that you as an employee remain aware of your environmental conditions and how to properly handle materials. The following information provides a general awareness of standard practices to prevent material related injuries.
- Materials Handling training
- Materials Handling Fact Sheet
- Ladder Safety Fact Sheet
- Lab Glassware Safety Fact Sheet
- Eliminate the need for manual materials handling
- Redesign the work task or environment
- Substitute manual materials handling for mechanical equipment
- Rest breaks and job rotation
- Wear appropriate personal protective equipment (PPE)
Office Workstation Ergonomics
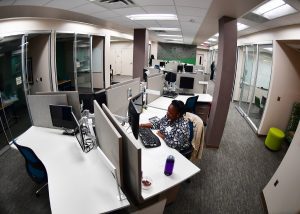
Repetitive motion is one of the leading causes of occupational injury at UNC Charlotte. These motions generally occur in the office work environment while using a computer workstation. Ergonomics is the practice of fitting the job to the individual, which can help prevent work-related musculoskeletal repetitive motion injuries. The following information provides general awareness of standard practices to prevent musculoskeletal related injuries due to repetitive motion.
- Computer Ergonomics training
- Office Ergonomics Self-Assessment Tool
- Eliminate the need for repetitive motion activities (Discuss with your immediate supervisor)
- Redesign the work task or environment (Conduct an Office Ergonomics Self-Assessment and/or enter a EHS Service Request)
- Substitute workstation equipment for more ergonomic friendly equipment (Contact Receiving and Stores at 704-687-5262)
- Rest breaks, ergonomic exercises, and job rotation
Heat Stress
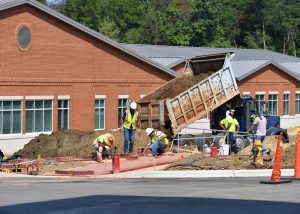
Heat Stress is one of the leading causes of occupational illness at UNC Charlotte. Therefore, it is very important that you as an employee remain aware of your environmental conditions and how to properly manage your heat exposure. The following information provides general awareness of standard practices to prevent heat exhaustion and heat stroke illnesses.
- Heat Stress training
- Heat Stress Fact Sheet
- Heat Safety App
- Eliminate the need to work in hot environments
- Redesign the work task or environment
- Substitute temperature controls indoor work environments
- Rest breaks and job rotation
- Wear appropriate personal protective equipment (PPE) for the work environment
Hand and Power Tools
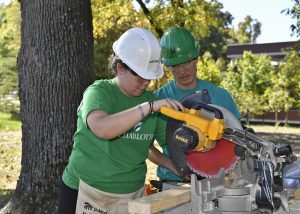
Hand and power tools are a common part of our everyday lives and are present in nearly every department. These tools help us to easily perform tasks that otherwise would be difficult or impossible. However, these simple tools can be hazardous and have the potential for causing severe injuries when used or maintained improperly. Special attention toward hand and power tool safety is necessary in order to reduce or eliminate these hazards. The following information provides a general awareness of standard practices to prevent hand and power tool injuries.
- Hand and Power Tool training
- Specific hand and power tool manufacturer’s manual
- Hand and Power Tool NCDOL Overview
- Eliminate the need to work with hand and power tools
- Ensure engineered guards and safety switches are working properly
- Substitute hand and power tools for other equipment
- Administer rest breaks, job rotation, equipment inspection, and maintenance
- Wear appropriate personal protective equipment (PPE) in accordance with the manufacturer’s manual
Job Hazard Analysis
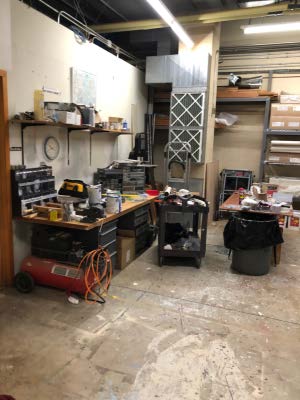
- What you need to know
- The value of job hazard analysis is to eliminate hazards and prevent work-related injuries. This is likely to result in fewer worker injuries and illnesses; safer, more effective work methods; reduced workers’ compensation costs; and increased worker productivity. The analysis also can be a valuable tool for updating ADA sections of job descriptions and training employees.
- The Office of Environmental Health and Safety has conducted job hazard analysis for jobs with the highest injury or illness rates and potential to cause severe or disabling injuries or illness.
- Submit a Health and Safety service request to have a job hazard analysis completed or to access the job hazard analysis library.
- What is a hazard?
- A hazard is the potential for harm. In practical terms, a hazard often is associated with a condition or activity that, if left uncontrolled, can result in an injury or illness. Chemical toxicity, electrical shock, electrical loss of power, ergonomics strain, excavation collapse, fall, fire, noise, radiation exposure, struck by, temperature, visibility, and weather are all common hazards. Identifying hazards and eliminating or controlling them as early as possible will help prevent injuries and illnesses.
- What is a job hazard analysis?
- A job hazard analysis is a technique that focuses on job tasks as a way to identify, evaluate, and control hazards. It focuses on the relationship between the worker, the task, the tools, and the work environment. Ideally, after you identify uncontrolled hazards, you will take steps to eliminate or reduce them to an acceptable risk level.
- What are hazard controls?
- Hazard controls are measures designed to effectively minimize hazards and associated risk. The five categories of hazard controls are as follows:
- Elimination: The most effective control measure that removes the hazard.
- Engineering: Modify existing machinery, equipment or facilities to isolate the employee from the hazard.
- Substitution: Substitute a substance, method or material to reduce the hazard.
- Administrative: Develop work methods or procedures to change the way employees work.
- PPE: The use of PPE as the main method to control exposures should be limited to situations where elimination, substitution, engineering, or administrative controls are not practicable, or when:
- Additional protection is required because other control methods are not sufficient to reduce the hazard
- The hazard is a result of a temporary or emergency condition
- Hazard controls are measures designed to effectively minimize hazards and associated risk. The five categories of hazard controls are as follows: